Program Facilitator
The facilitator for this program is Dr. Tariq Abdelhamid, CM-Lean. Tariq is Chief Lean Performance Officer with the Residential and Hospitality (RHS) Division at Michigan State University (MSU), where he is working with colleagues on a transformation journey to adopt Lean Thinking throughout RHS. He also holds an Associate Professor of Lean Construction appointment at the School of Planning, Design and Construction (MSU), where he teaches, conducts research, and routinely publishes on Lean Construction.
Tariq served as the Lean/IPD Coach for the Shaw Hall Dining Renovation project at MSU (Jan 2013), the first Integrated Lean Project Delivery project at a public university in the United States. Tariq also worked with the MSU Infrastructure Planning and Facilities group on a 3-year process improvement initiative titled Excellence in Campus Operations and Services.
Trained by Greg Howell and Glenn Ballard (founders of the Lean Construction Institute (LCI), USA), Tariq serves as chairperson of the LCI Academic Forum, is the Editor of the Lean Construction Journal since its inception in 2003, and is an LCI Research Fellow since 2016. He is also a Steering Committee member of the Lean in the Public Sector (LIPS) organizations (http://leaninpublicsector.org/) . Tariq was a member of the first AGC Lean Construction Steering Committee, and he was also involved as a subject matter expert and content developer in the AGC of America Lean Construction Education Program (2009-2013).
Tariq also works with Yokoten Consulting, Enovio Consulting, ReAlignment Group, and Gemba Kaizen Consulting on Lean Construction and Integrated Lean Project Delivery engagements with design and construction teams on projects of any budget size. Prior to joining MSU, he was trained and worked as a Lean Production subject matter expert for Ford Motor Company. He also worked as a Scheduler/Planner for PAC Project Advisors, and an Engineer III for the University of Michigan Construction Engineering and Management Office.
Overview
Lean Construction is concerned with aligning and connecting the understanding among different individuals across different spatial and temporal dimensions to get a structure built that meets the programmatic needs of the client. Lean is doing value-added work, per established standards/specifications and/or as mutually agreed by two or more parties, correctly the first time through, with the requirement of continually improving and respect for what people have to offer.
The Program
This program is a 5-day immersion in the emerging discipline of Lean Construction. The program features a seven-unit series intended for those individuals who will design and implement a lean transformation strategy within an organization, and those leading projects using lean project delivery. This 35 – hour program was developed to help you obtain the Associated General Contractors (AGC) of America Certificate of Management - Lean (CM-Lean). This is a recognized credential that acknowledges that its holder is knowledgeable in Lean Construction areas of competency.
Earn Your Lean Credential
Following completion of all seven units of the Lean Construction Education Program, participants will be qualified to sit for an exam to earn AGC’s CM-Lean.
Who Should Attend
Architects, Designers, Contractors, Construction Managers, Suppliers, Service Providers and professionals seeking additional information about Lean Project Delivery, or those interested in obtaining their CM-Lean credential.
Learning Objectives
The overall aims of the LCEP are to:
1. Develop Lean Construction champions within an organization
2. Advance the use of lean practices in construction through development of a consistent nomenclature and practices
a. Describe lean principles and culture and give examples of their application in design and construction.
b. Describe how leading construction companies use Lean Construction to consolidate materials and utilize just-in- time to avoid bottlenecks on site.
c. Discuss and apply the basics of the Last Planner® System: a project planning and production control.
d. Explain the Lean Project Delivery in practice using relational contracting methods.
3. Provide an industry-recognized credential that creates a common standard of knowledge
Program Outline
Day 1 AM: Variation in Production Systems (Unit 1): In the construction process, the work we do is all connected and variation in even one of those processes affects us all. This course provides tools to help recognize sources of variation on projects, examine variation’s effect on operations, and mitigate the effects of variation in every-day work.
Following completion of this course, participants will have the ability to: define the different types of variation; explain the concept of throughput and distinguish it from productivity; discuss the role of variation in production operations; list sources of variation in construction settings; and explain and contrast variation mitigation techniques.
Day 1 PM: Pull in Production Systems(Unit 2): The course introduces the concept of pull as a means to reliable workflow and the advantages of pull production systems over traditional push and batch and queue systems.
Program Outline
Day 1 PM: Pull in Production Systems(Unit 2):
Following completion of this course, participants will have the ability to: compare batch-and queue and continuous-flow production systems; distinguish push systems from pull systems; describe the impact of pull in production systems; and explain pull strategies in construction operations.
Day 2 AM: Lean Workstructuring (Unit 3): The course introduces an essential component of the Last Planner® System, Lean Workstructuring (LWS). The course includes a building simulation activity to familiarize participants with pull planning, denotes the difference between push and pull planning, how LWS differs from other methods, and outlines its products briefly for the pre-construction and construction phases. Following this course, you will be able to: apply the methods and tools utilized in pull planning; describe the concept of Lean Workstructuring; outline the desired products of Lean Workstructuring; describe the characteristics and application of the Last Planner® System settings; and explain and contrast variation mitigation techniques.
Day 2 PM: The Last Planner® System (Unit 4): Unit 4 is the second of two units introducing the Last Planner® System (LPS®) – a project planning and production control process that asks for commitments and promises from team members to meet the overall target schedules. This course includes a building simulation activity, working backwards with sticky notes, to familiarize participants with all LPS® associated practices, namely, Phase Planning, Make Ready Planning, and Weekly Work Planning levels including percent plan complete calculations. Case studies are discussed to emphasize the underlying principles in LPS®. Following this course, participants will be able to: apply the Last Planner® System on a project; hold make ready and weekly work planning sessions; and calculate, track and analyze percent plan complete for a project.
Day 3: Lean Supply Chain and Assembly: This full-day course that introduces the lean strategies and tools used to deliver materials, equipment and prefabricated assemblies to the jobsite in a manner that facilitates flow. The course challenges class participants to map the supply chain - looking to minimize waste and maximize value - in a collaborative fashion with all project team members, including suppliers and vendors. Following this course, participants will be able to: differentiate between traditional procurement practices & lean supply chain applications; identify waste & value-adding activities within the supply chain & assembly; evaluate the impact of using lean supply chain on waste elimination, continuous flow & site operations pull; expand lean beyond the individual project; and more.
Day 4 AM: Lean Design & Preconstruction: This course explains the concepts of value-based management, lean in the design process and relational contracting. The course is divided into three sessions and teaches participants to: distinguish between the varying definitions for design; define value and commonly used methods to maximize it; discuss waste and commonly used methods to minimize it; differentiate between traditional project methods and lean design; and explain the various lean tools used in design and how to deploy them.
Day 4 PM and 5 AM: Problem-Solving Principles and Tools: A seven hour course that describes the Lean Problem Solving Process and illustrates how to use tools to solve problems in a lean manner. Following this course, you will be able to: define the difference between traditional and lean problem solving; describe how to create a team environment to solve problems; explain how to create trust to avoid problems; describe Observation Walks; identify root causes of problems, and develop an A3.
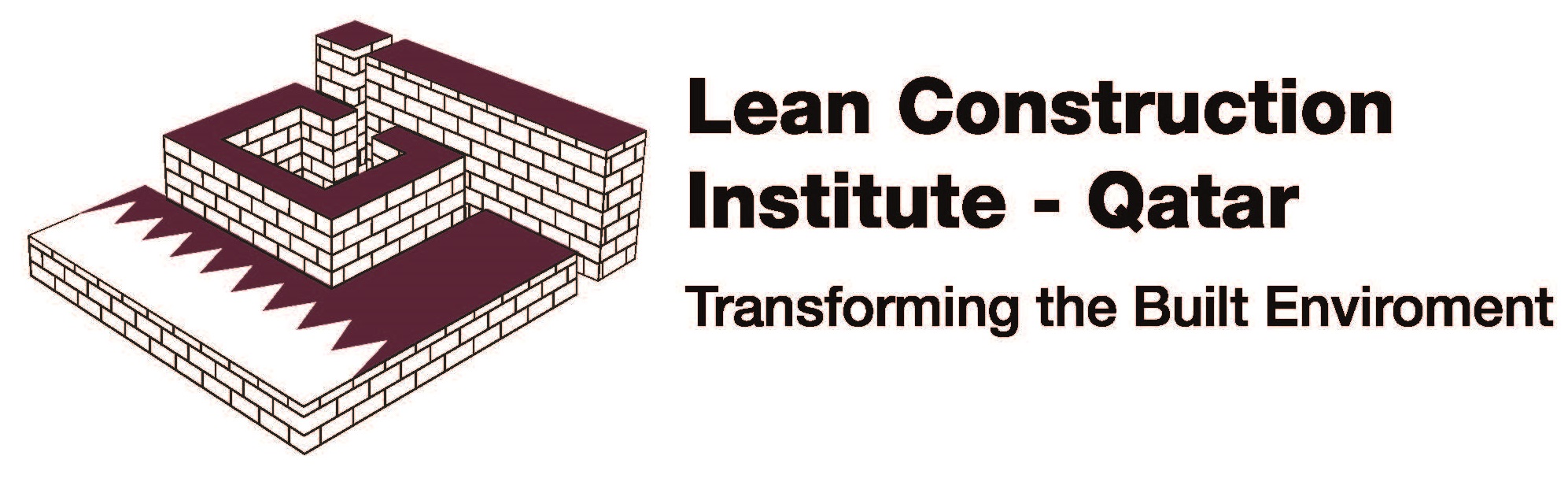